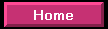
|
INTRO
to ENGINEERING PAGES
Research and development in the
engineering sciences is a huge undertaking, carried out by many tens of thousands of
professionals. We have synthesized and organized some of the disciplines that are very
promising and very important. While no one can predict where and how far each technology
will evolve, it may be possible to obtain an aggregate picture of important groupings and
therefore of where near-term progress is likely.
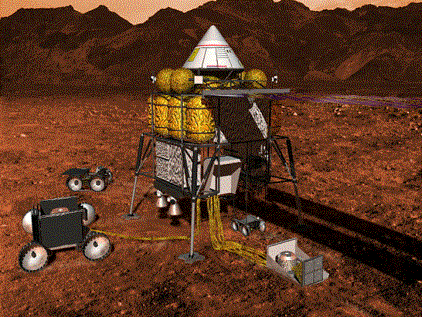
Information
has been obtained from public sources, in particular, from the pages of research interests
of the program managers of the US National Science Foundation, http://www.nsf.gov/,
AFOSR, http://www.afosr.af.mil/,
ARO, http://www.aro.ncren.net/main1.htm,
ONR, http://www.onr.navy.mil/
and NASA, http://ails.arc.nasa.gov/AILS.html
. These pages and the information therein are all public record.
By gathering these interests in one location, we hope to publicize the important work of
these program managers in organizing a major portion of the research base of the United
States, and to inform our readers of where current thinking is on technological and
scientific progress. Most industrially sponsored research tends to be proprietary. One may
expect, however, that the areas described below are representative of the
state-of-the-art.
For our academic readers, these pages may suggest lines of research that are worth
pursuing. Perhaps links between currently disjoint areas of research will become evident.
Such research at the boundaries between disciplines can be very rewarding and should be
pursued. For our industry-based readers, we hope that by viewing where engineering
research is focusing its efforts, industry can look further ahead to where opportunities
wait for innovative development. Perhaps some of the technological pushes being described
in these pages can be merged with existing products and internal R&D, leading to the
next product, or better yet, the next product line.
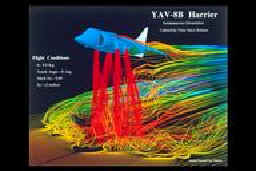
Various engineering disciplines will be presented. The discussion is geared to the expert.
Also, look for information on specific products in the near future.
* *
*
We welcome proposals from our readers
to write
specialist essays on
their areas of technical
expertise.
* *
*
FLUID MECHANICS
Introduction
(Army)
The performance of Army weapon systems that involve airborne vehicles or convecting
liquids is greatly affected by the fluid motion and the resultant forces imparted to the
vehicle. The study of fluid dynamics is, thus, of vital interest for the design,
development, and performance enhancement of many Army systems. One weapon system important
to the Army is rotorcraft vehicles, whose performance depends largely on a mature and
sound understanding of the fluid dynamics of such vehicles in flight. This field of
aerodynamics makes possible the tactical flight operations envisioned for the highly
mobile Army of the 21st century.
The goal of more accurate, stable, maneuverable, and longer-range munitions dictates the
need for aerodynamics research for both gun-launched projectiles and tactical missiles.
Flow Separation
Flow separation plays an important
role in limiting the performance of many Army systems. Unsteady separation of
boundary-layer fluid on the suction side of rotorcraft blades leads to dynamic stall on
the retreating side of the rotor disk, with an attendant loss of lift and large negative
pitching moment. Dynamic stall can be thought of as the pacing technical item inhibiting
the development of agile super-manueverable rotorcraft. Flight regimes directly affected
by this phenomenon include air combat, terrain following the nap-of-the-earth, and
shoot and scoot. Missile and projectile base and afterbody flows often involve
flow separation caused by control surfaces, shock waves, or discontinuous changes in body
contour. Clearly, a thorough understanding of the various fluid dynamic mechanisms
underlying flow separation can be used to tremendous advantage in the design of future
Army systems, and the trend in the fluid dynamics program is to apply this fundamental
knowledge to control this phenomena.
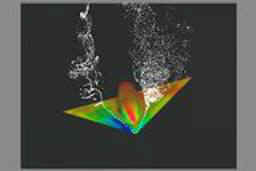
Accurate performance prediction of Army missiles and projectiles requires the ability to
accurately predict the flowfield in the base region of these devices. While the modern
techniques of computational fluid dynamics have made great contributions in this area,
they are limited by the lack of accurate nonequilibrium turbulence models. It is difficult
to formulate such models even for situations in which the flowfield has been well
documented. In the case of missiles and projectiles operating at transonic and supersonic
speeds, quantitative experimental measurements of the base-region flow are exceedingly
difficult to perform accurately, and the task of the development and selection of adequate
turbulence models is extremely challenging.
Nonintrusive Flow Diagnostic Methods
Research within the area of fluid
dynamics over the last decade has resulted in the conception, development, and validation
of a wide array of powerful new tools. In the experimental arena, the development of
nonintrusive flow diagnostic methods, such as particle imaging velocimetry (PIV),
holographic interferometry, and luminescent paints, is revolutionizing the study of fluid
mechanics.
Computational Method
Computationally, developments such as unstructured and Chimera grids, direct and large
eddy simulation (LES), and high-speed parallel computers, have provided the capability to
analyze complex fluid dynamics problems which previously were not amenable to analysis.
Advances in smart materials, microelectromechanical systems (MEMS), fuzzy logic, and
neural networks offer the possibility of fluid mechanics control for a variety of Army
systems. The application of these new tools to important Army fluid dynamics problems
enables significant performance and life cycle cost improvement for many Army systems.
Research within the Fluid Dynamics Program is focused on the use of these tools for
fundamental understanding of the complex fluid dynamics processes underlying these systems
and involves analytical, computational, and experimental approaches.
Rotorcraft
Increased performance demands on
modern Army rotorcraft require the accurate prediction and control of the forces and
moments generated on the vehicle in hover, forward flight, and maneuver. Accomplishing
this broad objective requires, for example, research into the mechanisms underlying
unsteady separation of boundary-layer fluid on the suction side of rotorcraft blades,
wakes, unsteady rotor aerodynamic loads, interference aerodynamics, and computational
fluid mechanics. Typical examples of ongoing research within this field are the
experimental and numerical determination of the flowfield over airfoils undergoing two-
and three-dimensional unsteady separation with subsequent dynamic stall, the use of
nonintrusive experimental techniques, and the development of efficient computational
methodologies to accurately determine the flowfield induced by the main rotor on the
helicopter fuselage- empennage-tail rotor, and the development of advanced rotor free-wake
methods to improve predictive capability for helicopter performance, vibration, and noise.
Projectiles
To ensure the accuracy and range of
unguided gun-launched projectiles and the maneuverability and lethality of guided
munitions and rockets, a thorough knowledge of the forces and moments acting during both
launch and free flight is required. These objectives dictate research on shock
boundary-layer interactions, compressible turbulence modeling, aft body-plume
interactions, vortex shedding at high angle of attack, transonic body flows, and
aerodynamic interference effects between various missile components. The general research
areas of turbulent flows on spinning bodies, multi-shocked flowfield structure, base drag
analysis and reduction, and control jet-flowfield interactions are also relevant to this
research program. Examples of current studies in this subfield are the experimental study
of aft body-plume-induced separation, the use of direct numerical simulation, LES,
laser-Doppler velocimetry (LDV), and PIV techniques to investigate axisymmetric supersonic
power-on/ power-off base flows, and the experimental investigation into the underlying
physics of unsteady shock-wave /turbulent boundary-layer interactions.
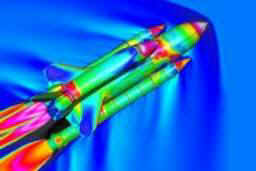
Introduction (Air Force
Air Force basic research in fluid
mechanics seeks to enhance the performance and reliability of aerospace vehicles by
developing new capabilities for predicting and controlling the fluid dynamic and
thermodynamic behavior of complex flows in flight regimes and propulsion systems affecting
Air Force operations. This research seeks to understand essential physical phenomena, to
develop methods and models to predict them, and to create innovative strategies to expand
the boundaries of flight by controlling these phenomena.
Major thrusts include: 1) the development of
computational methods for accurate and efficient numerical solution of
the equations of fluid dynamics, especially for dynamic, unsteady, multi-body problems, 2) active flow control relevant to engine nozzle
exhaust flows, mixing thrust vectoring, and high lift, 3) the aerothermo- dynamics of hypersonic flows, 4) the fundamental structure and dynamics of
transitional and turbulent compressible flows, 5)
the prediction and control of turbulence, and 6)
the complex internal aerodynamics and thermodynamics of flows in gas turbine engines.
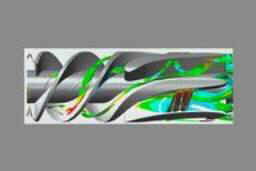
Turbulence
Aircraft manufacturers, AFRL directorates and test centers require improved, validated turbulence models. In fact,
such models top the list of industry needs for fluid
mechanics research and are a key pacing item for computational fluid dynamics.
Research targets the high Reynolds number, compressible flows of interest to the Air
Force, and seeks to develop large-eddy simulation (LES) methods and improved subgrid
turbulence models for accurate predictions.
* * *
turbulence
models top the list of industry needs for fluid mechanics research and are a key pacing
item for
computational fluid dynamics
* * *
Aircraft and weapon systems in
maneuvering combat operate in environments far more hostile than those occurring
under level flight. Weapons released in this environment have been known to hit the launch
aircraft. Advanced Computational Fluid Dynamics (CFD) research is developing numerical
simulation methods that predict the dynamic motion effects on aircraft systems and
missiles. Research in multi-body CFD is developing computer simulation technology that can
predict the trajectories of weapons as they release from an aircraft, reducing the danger
to pilots who fly weapons certification tests. CFD research also focuses on understanding
the fundamental causes of inlet unstart, the sudden shut down of engines on maneuvering
supersonic and hypersonic vehicles.
Active Flow Control
Active flow control research
explores fundamental flow instabilities and their control for potential application to
thrust vectoring, engine controls, high lift, aero-optics, low noise, and several other
critical areas. Low observable requirements fix jet nozzle exit geometry and require
internal flow adjustments to optimize performance. Fluidic flow controls are being
explored in this context. Innovative active flow control approaches also enable the
development of advanced high-lift technologies for enhanced aerodynamic performance of
stealth vehicle configurations. Active flow control may also alleviate currently
uncontrolled sonic fatigue problems with the divergent nozzle flaps; those on the F-110
engine create one of the major headaches for logistics support of the F-16. Also,
inadequate turbulent drag reduction strategies limit the potential for enhanced range and
payload. Basic research approaches under exploration include innovative uses of
microelectromechanical systems (MEMS) and neural networks, the generic issue being the
management and control of vorticity production on aerodynamic surfaces. McDonnell Douglas
is now exploring basic research results on jet control for supersonic jet noise reduction,
fluidically controlled thrust vectoring, and paint removal processes. Boeing is exploring
new aerodynamic testing
methods based on recent basic research on microfabricated flow sensors.
Hypersonic Flight
Future hypersonic flight vehicles will operate at very high altitudes within the earth's
atmosphere to reach global targets. At these altitudes, the atmosphere is highly rarefied,
and it is important to predict the character of these rarefied flows. Underpredicted drag
and heat transfer can result in vehicles that will not reach their intended targets.
Computational and experimental research aims at revealing the fundamental fluid mechanical
properties of hypersonic, chemically reacting flow, providing better predictions of
vehicle heating, directly leading to safe designs.
3D Flows
Maneuvering combat aircraft generate complex, 3-D spatially and temporally varying flows
that are ingested by the propulsion system's airbreathing engine inlets. The total
pressure distribution of these complex flows entering the inlets become even more
non-uniform, or distorted, as the flow passes through the inlet compression shock wave
system. This distortion greatly reduces the total pressure of the flow that enters the
compressor face for supersonic propulsion and turbomachine engine propulsion systems. The
greater the distortion, the lower the engine thrust. Computational fluid dynamic research
has been undertaken to predict the complex distortion fields which arise in supersonic and
hypersonic air breathing engine inlets and inlet systems on maneuvering Air Force aircraft
and missile weapons systems.
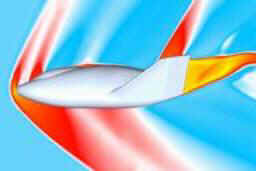
Flight Control
Current flight control systems intentionally limit the operational envelope of modern
fighters to avoid entering the post stall environment during dynamic maneuvers. Unsteady
aerodynamics research within this project seeks to develop the knowledge base to expand
the predictability and controllability of flows in this environment. Another critical need
is preventing the unsteady aerodynamic buffeting of vertical control surfaces on the F-15
and F-16 that leads to structural fatigue, loss of reliability and degraded
supportability.
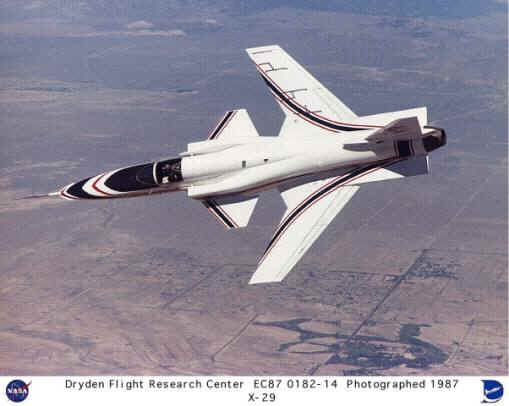
Engine Technology
A major concern of engine manufacturers, and the focus of the Integrated High Performance Turbine Engine Technology
(IHPTET) Program is to improve the thrust to weight ratio of gas turbine engines. Improved
compressor efficiency and stability are essential elements of this requirement. Problems
with heat transfer in the combustor and turbine stages account for half the ten-year
development time currently required for new engines. In addition, thermally induced
fatigue failures in the F-110 combustor produce one of the largest maintenance problems
for the F-16. Research within this project aims at improving our understanding of heat
transfer in high turbulence environments, improving film cooling, and controlling the
unsteady fluid dynamics dominating compressor performance and contributing to the problem
of high-cycle fatigue.
Joint DoD Cooperation
Through Joint DoD Cooperation, this Air Force research program is closely coordinated with
Army and Navy programs. AFOSR fluid mechanics research focuses on central Air Force
interests in high speed flows, compressibility, dynamic maneuverability, control of
aerodynamic phenomena, and the fluid mechanics and thermodynamics of flow in gas turbine
engines. In turn, the Navy focuses on hydrodynamic wakes and free surface phenomena. In
the area of unsteady aerodynamics, the Army deals primarily with 2-D blade-rotor
interactions relevant to helicopters, while the Air Force focuses on 3-D vortex dominated
fluid-structure interactions relevant to aircraft maneuverability.
SOLID MECHANICS
Introduction (Army)
Army systems and subsystems are designed for prescribed lethal effects and maximum
protection levels along with agility and mobility at affordable costs. They are subjected
to long-term effects under benign circumstances, as well as short-term catastrophic
effects under hostile field conditions. Choices among a complex array of materials and
manufacturing processes need to be made for the optimum tactical and logistical
superiority. The flow, instability, and failure behavior of materials and structures under
stresses caused by hygroscopic, thermal, mechanical, chemical, and electromagnetic
constraints critically determine the future capabilities of our fighting forces.
* *
*
the flow, instability, and failure
behavior of
materials an structures under stresses critically
determine the future capabilities of our fighting forces.
* *
*
The science of solid mechanics transforms the physical phenomena (deformation,
instability, and failure) into algorithms for simulation codes through self-consistent
mathematical constructs based on clean, tractable, laboratory-scale experiments. The
products of fruitful research in solid mechanics are the models, which are integral to,
but hidden in, the simulation routines. The reliability of displayed results, which are so
important in design decisions, is never better than the ability of the model to portray
the event as realistically as possible. Fundamental developments in solid mechanics are
augmented by developments in physics and materials science, in diagnostic techniques to
probe micromechanical phenomena, and in computational mechanics.
The major areas of interest for the U.S. Army Research Office (ARO) Solid Mechanics
Program are micromechanics, finite deformation, instabilities (such as shear localization and
cracks), stress wave propagation, damage mechanisms, and computational techniques to handle heterogeneities,
steep gradients, and discontinuities. The results have applications to armor/anti-armor,
weapons platforms, ammunition, and survivability considerations of Army materiel and
personnel.
Failure and Damage Mechanisms
A thrust area of particular importance to the Army in the solid mechanics field is failure
mechanism determination, assessment, and damage effects on structural performance.
Particular emphasis is placed on structures performing in complex and aggressive loading
environments where the coupling between micromechanics and overall material response must
be considered in the design of more reliable Army equipment. Typical subject areas
requiring emphasis are three-dimensional constitutive models that allow for path
dependency, localization phenomena, failure processes induced by aggressive service
environments, and the effect of many interacting inhomogeneities in structural materials.
Scaling laws and the understanding of stochastic behavior in composite structures are
potentially important topics to the Army.
Large amounts of deformation through nonproportional multi-axial loading paths are
encountered in the fabrication of many armaments / missiles components, in the formation
and flight of explosively formed penetrators (EFP) and shaped charge jets, and in the
penetrator / target interaction zones. Conditions of strain rate and temperature are also
heterogeneous. Nonlinear processes, such as the nucleation and growth of shear bands, are
performance-limiting in some instances and are to be promoted in others. Understanding and
parametric analysis of these processes is facilitated by the development of constitutive
models and failure criteria. Rate-dependent
finite deformation plasticity theory,
evolution of texture, criteria for formation of shear bands, and nucleation, growth, and
coalescence of voids and cracks are important technical issues.
Composite materials are serious contenders for a variety of Army materiel because of their
superior stiffness and specific strength. They are also prone to defects during processing
and service. Nonlinearities in structure-dependent behavior of these heterogeneous
materials make design techniques, scaling, and service-life predictions very difficult but
important issues.
Selected current research studies pursued in support of these areas in solid mechanics are
experiments, analytical modeling, and numerical simulation of evolution of damage in
structures; crystal plasticity and continuum treatment of large deformation at high strain
rates; experimentally verified models for probability of failure modes in composites; high
strain-rate deformation and failure in dual-phase composites; nonlinear behavior of
functionally gradient materials; and micro-mechanics of anisotropic solids with
inhomogeneities and cracks.
Impact and Penetration
Another major thrust is the
determination of impact and penetration processes in both homogeneous and composite
structures with special focus on the high strain rate phenomena and the resulting material
failure sequences. Penetration mechanics is a subject that integrates the development of
many subjects to provide a predictive capability. Physical understanding of the processes,
models which can be simply verified in laboratory scale experiments but can be applied to
field experiments by simulation, and numerical experiments with innovative techniques in
computational mechanics are worthy of research pursuit.
A wide variety of Army materiel, such as helicopter blades, tactical missile structures,
ground vehicle armor, and penetrators, are often subjected to impact loading covering the
full spectrum of impact velocities and impulses. Vulnerability assessments and design of
space- and weight-saving protection systems depend on understanding the mechanics of the
phenomena. Ever-increasing demands for weight and volume efficient protective structures
for armored vehicles need to be addressed by making use of every possible mechanism in traditionally passive materials. Energy absorbing
mechanisms can be triggered by the stresses due to impact or disruptive mechanisms and can
be instigated by external means in materials to affect penetration mechanics. The intent
is to create a science base necessary for the exploitation of novel materials/mechanisms.
Topics in this area include stress wave propagation in solids, damage evolution in
brittle/ductile materials, impact damage and penetration processes, and structures that
retard the penetration process. Selected projects in the impact and penetration research
area are focused on shear resistance and shear localization under high-pressure at very
high rate for high-strength steels, tungsten alloys, and tantalum; finite element
simulation of the penetration process in cases of depleted uranium (DU) or tungsten alloy
through steel; failure criteria and failure mode transition in ductile materials;
mechanics of long rod penetration into ceramics under confinement; materials modeling of
shock-induced chemical reactions in nonenergetic powder mixtures; shock wave propagation
through layered media; and shock-induced phase transformations.
STRUCTURES and DYNAMICS
Introduction (Army)
The interaction of inertial, elastic,
impact, damping, and aerodynamic forces acting on armament systems, rotorcraft, missiles,
and land vehicles is of fundamental importance to the design and construction of reliable,
durable, and maintainable Army equipment with acceptable levels of personnel safety and
comfort. As advanced weapons and mobility systems evolve to meet the demanding
requirements of higher acceleration levels, greater loading rates, higher temperatures,
and increased relative velocities among system components, greater attention must be
devoted to the development of effective, high-quality military equipment that will
withstand extreme battlefield conditions.
Thus, designers must assure the integrity of structures and machine components through an
understanding of the stress and deformation states that result from a variety of complex
loading mechanisms in the static and dynamic regimes. This understanding can be attained
through the development of sophisticated mathematical models and effective, efficient
numerical solution techniques validated through extensive experimental investigations.
Consequently, ARO supports fundamental research in structural mechanics of composite
materials, structural dynamics, control, simulation, and smart structures.
Of special interest is the new field of smart structures concepts applicable to the armor
environment. Such resilient structures would combine the functions of sensing, actuation,
and control in the space and time domain necessary to autonomously react to the impact and
penetration event characteristic of armor attack, to provide resistance to the
penetration/failure processes. Examples of phenomena to be examined for these innovative
applications are shock-induced material reactions and resultant chemically changed
compositions, phase transformation effects, and electro-thermomechanical processes that
can be beneficially used for energy soak mechanisms.
Undesirable vibration levels occur in a variety of equipment used by the Army. An
effective, innovative approach to quench such structural vibrations is the development of
smart structural components that can automatically compensate for the excessive force
levels applied to them. The concept of a smart structure is based upon the application of
modern control techniques to structural elements fabricated from composite materials, in
which actuators and sensors are embedded. Because of their directional strength
properties, passive and smart composite structures can be tailored by engineers to
optimize their dynamic response characteristics.
Structural Damping Techniques
Significant progress is also being made in the development of novel structural damping
techniques that could have a significant effect on how helicopter rotor blades and weapons
systems are designed. New schemes currently under investigation include
magneto-rheological and electro-rheological fluid based damping devices, active
constrained layer damping treatments, piezoceramic actuators bonded to a structure and
coupled to a shunted electric circuit, and nonlinear controller facilitated energy
dissipation through an electronic circuit. Other new approaches, such as distributed
control techniques (in contrast to controllers for discrete systems), localization and
isolation of modal response, delayed action vibration absorbers, and neuromuscular-like
control for absorbing structural vibration energy, may offer opportunities for progress in
vibration control in the future.
Structural Mechanics of Composite
Materials
Engineers require refined theories of elastic structures and improved, precise, and
efficacious analytical and numerical procedures to design complex structures, frequently
fabricated from advanced composite materials that can endure, without structural failure,
repeated intense static and/or dynamic loading regimes. Many modern mechanical systems
consist of combinations of rigid and deformable structural components that are lightweight
and strong, but sometimes brittle. Therefore, a highly relevant problem is that of the
mathematical modeling of anisotropic and laminated composite beams, plates, and shells.
The new theory under development features the inclusion of geometrically exact kinematical
equations, accounting for the presence of delaminated zones, and a general sectional
modeling analysis methodology. This research offers the Army the capability of analyzing
the static and dynamic behavior of highly complicated structures, such as those used in
land vehicles and helicopter rotor blades.
The helicopter and automotive industries are today using composite materials in their new
vehicles more frequently than previously because of their great strength, relatively
lightweight, and advantageous thermal and electrical conductivities. The experienced load
spectrum in the Army application is extremely broad. Fiber reinforced composites are being
studied for use in hingeless and bearingless helicopter rotor blades. These blades can be
used with rotor hubs that are significantly less complicated and expensive than the
mechanically complex hubs currently in use with articulated rotor blade systems.
Aeroelastically tailored composite rotor blades offer significant potential for improved
stability, reduced vibration,
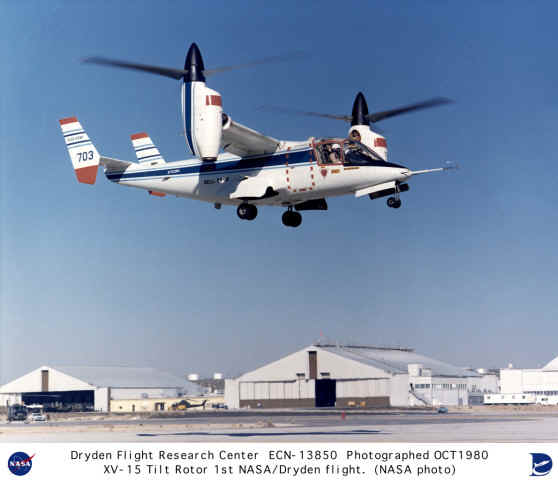
simplified hub design, and
improved handling qualities of rotary wing vehicles. Advance- ments in each of these
fundamental technical areas can lead to enhanced reliability, maintainability, personnel
safety, and system performance. Development of new analytical tools to predict the complex
dynamic behavior of these rotor systems is essential to the successful integration of
tailored blade technology into next generation rotorcraft systems.
As an example of timely research in this area, a current investigation is focused on the
development of a new composite rotating box beam model (for helicopter rotor blades) with
embedded piezoelectric actuators based on a refined higher order laminate theory. The theory includes the effects of
imperfections such as delamination and debonding of actuators. Analytical and numerical
results reveal that embedded piezoelectric actuation significantly reduce the deflection
along the box beam span and can be used to control the magnitude of blade vibrations. In
extreme cases, the actuation can compensate for almost all deflections along the span due
to blade weight and external loads.
Structural Dynamics and Simulation
This area of activity is focused on ground vehicle and multi-body dynamics, structural
damping, structural controls, and inflatable structures. Key problems are the
determination of the transient and steady state response of structures that are subjected
to forces such as gravity, damping, aerodynamic influences, and electric fields. Because
of the magnitudes of the loads exerted on Army equipment and the need to reduce weight to
enhance performance and range, it is essential to include the deformation characteristics
in the mathematical models developed to describe system behavior. Numerous large and
complex mechanical systems used by or for the Army consist of interconnected multi-body
structures, such as heavy machinery, wheeled/tracked military land vehicles, robotic
equipment, machine tools, rotorcraft, vehicle engines, power transmissions, communication
devices, and automatic weapons. To design such structures efficiently and effectively,
kinematic and dynamic simulations of flexible multi-body systems based on constrained
non-linear dynamics are required. In particular, recent advances in computers, graphics,
and communication are undergirding recent developments in motion based simulators with
computer generated imagery that interface vehicle dynamic models and their physical
environments.
Such computer simulations predict the
kinematic and dynamic behavior of multibody systems in considerable detail, providing
sufficient data to study the influence of a variety of design parameters and to determine
the detailed evaluations of concept performance capabilities. Examples of current research
programs include the development of (1) a
non-linear dynamics analysis of tracked vehicles that includes the interaction between the
track links and the ground, the sprockets, the idlers, and the rollers of the tracked
vehicles; (2) a novel active structural damping
technique using piezoceramic actuators and non-linear controller concepts to suppress
transient and steady bending and torsional vibrations of flexible structures; and (3) a refined analysis capability for electroded
piezoelectric plates, which yields highly numerical values of resonance frequencies for
AT-cut quartz plates that are desired for advanced radar and communications systems
because of their frequency stability against temperature fluctuation and acceleration
induced stresses.
Smart Structures
A smart structure is defined to be a structure that contains embedded sensors and
actuators with associated control system capabilities enabling it to respond in real time
or nearly real time to external stimuli in proportion to their intensity to compensate for
undesired effects or to enhance desired effects. The application of the smart structure
concept offers the potential for the development of a new series of structural systems
that may find application in modern rotorcraft, land vehicles, weapons systems, aircraft,
submarines, spacecraft, and industrial machinery. To realize the promise of such active
structures, additional research is required into the fundamental understanding of how they
function and how they can be controlled. Hence, engineers and designers must know how to
create the next generation of active materials that can serve as effective sensors and
actuators, how to express appropriate constitutive equations, how to derive their
equations of motion, how to design efficacious controllers, etc. This knowledge will
permit Army engineers to suppress the vibrations in machine gun barrels and rotorcraft
structural components; augment aeromechanical stability; enhance rotorcraft handling and
maneuverability qualities through the change of a rotor blade's camber; reduce
blade-vortex interaction noise levels in rotorcraft; and detect structural damage, such as
material fracture, debonding, and delamination.
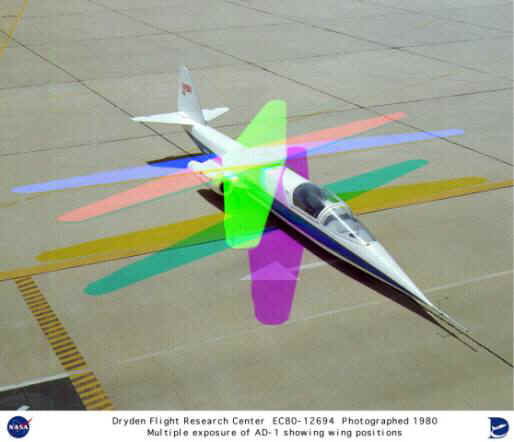
* *
*
The application of the smart
structure concept offers the potential for the development of a new series of structural
systems that may find application in modern rotorcraft, land vehicles, weapons systems,
aircraft, submarines, spacecraft, and industrial machinery.
* *
*
The most prominent actuation techniques suggested for smart structures are based on the
properties of piezoelectric ceramics and films, shape memory alloys (such as nitinol),
electro-rheological fluids, electrostrictive materials, and magnetostrictive materials
(such as terfenol-d). However, it may prove necessary to devise hybrid actuators formed by
combining the properties of two or more actuating substances or to consider optimized
actuator configurations that deliver greater force or displacement levels.
As an example of research in this
area, researchers are developing a layered piezoelectric actuator in a semi-circular or
C-shaped configuration that produces greater force and deflection levels than conventional
piezoceramic stacked or flat bimorph actuators. It is being tested in an active helicopter
rotor blade flap system, where it will be used in higher harmonic or individual blade
control systems. These C-shaped actuators can be arranged in series and/or parallel to
tailor the force and deflection generated. This C-shaped actuator will produce flap
deflections sufficiently large (up to ±10) to provide significant reductions in rotor
blade vibration amplitudes. The actuator model is generic and can be used to design
optimized C-shaped actuators for missile flap control surfaces for flight control and
suppressing vibrations of machine gun barrels.
Recent research has revealed that
composite structural materials with embedded shape memory alloy wires offer significant
increases in energy absorbing ability and penetration prevention capability. Experiments
revealed that the shape memory alloy wires have a considerable effect on the load
deflection behavior. For example, a 41 percent increase in absorbed energy over the
bi-directional plain graphite lay-up was observed in the 6 percent volume fraction
unidirectional shape memory alloy bi-directional graphite hybrid. These configurations
offer penetration prevention but not increased damage resistance. Therefore, they have
potential use in such applications as personal body armor and lightweight shelters.
Solid Mechanics and Structures (Air
Force)
This area of research seeks to develop a fundamental understanding of the behavior of
aerospace materials, structures, and supporting facilities, leading to the cost-effective
development and safe, reliable operation of superior weapons and defensive systems.
Research includes such diverse topics as the micromechanical design of advanced materials,
modeling and simulation of the dynamic behavior of aircraft, missiles, earth penetrators,
airfield pavements/facilities, and large space structures, and the technology integration
for the performance and survivability enhancement of these systems.
The mechanics research sponsored in this project is closely coordinated with research
performed under Structural Materials, which considers the materials science processing
aspects of modern aerospace structural material systems, and research performed under
Fluid Mechanics, which considers basic research issues associated with turbulence modeling
and hypersonic flight.
Future aerospace engine and airframe structures will be composed of advanced, fibrous
materials capable of extended operation in severe environments. Research in the mechanics
of materials area seeks to understand the fundamental behavior of these material systems
to facilitate the development of accurate design and life prediction methodologies. The
development of these materials will allow the design of faster, more efficient aircraft
and spacecraft. These advanced materials are also enabling technology for future Air Force
initiatives such as hypersonic aircraft, which can potentially take off from conventional
runways and achieve global orbit, and highly maneuverable uninhabited aerial vehicles (UAVs). Current project thrusts
include understanding the fracture behavior and thermomechanical behavior of high
temperature composite materials, such as ceramic- matrix composites, metal-matrix
composites, carbon-carbon composites.
Scientific issues include improved fiber/matrix interfaces, durable coating systems, and
improved design methodology and life prediction systems based on material damage growth
mechanisms. Results from this program are being used by Northrop-Grumman to understand
matrix cracking and fiber/matrix interface failure in ceramic-matrix composites. AFOSR
researchers are also studying innovative heterogeneous material systems, such as textile
composites, functionally-graded materials and nanostructural materials as well as
functional materials for smart structure applications.
Service Life
The extended service life for many existing systems also requires further research to
understand how materials and structures behave after very long periods of service. Factors
such as corrosion and multiple-site damage serve to reduce the load-carrying capability of
aging Air Force aircraft. This area seeks new methods of nondestructive evaluation (NDE)
of these systems to detect internal cracking and/or corrosion in a quick and reliable
manner, and to provide improved life prediction methodologies. Results from this research
are being used by the Air Force Research Laboratory to understand the effects of corrosion
and fatigue on the safety of aging aircraft structures.
Particulate Systems
The goal of the particulate and fluid mechanics research program is to develop a first principles understanding of the
behavior of particulate systems and their interaction with the surrounding environment.
The first principle thrust focuses on understanding the mechanical behavior of multiphase
particulate systems. Particulate materials are defined as those that can be represented as
an assemblage of physically discrete particles - either alone or in a matrix material
having significantly different properties. Particulate materials of interest include
soils, rock, concrete, asphalt, and engineered nanoparticles.
The specific research objectives are to understand: 1)
the influence of material microstructure on overall macroscopic constitutive behavior; 2) the constitutive behavior of multiphase
(heterogeneous) particulate systems; 3) the
localization and instability in particulate media, including their potential to flow and
liquefy; 4) effects of material interfaces; 5) damage accumulation and penetration mechanics of
geomaterials; 6) effects of new chemical
compounds released into the subsurface environment; and 7) transmission and attenuation of electromagnetic
and seismic waves in geomaterials.
Particulate mechanics research examines particulate systems with characteristic lengths that range from nanometers to
meters. Efforts seek to obtain quantitative relationships to describe the fundamental
mechanics governing the behavior of particulate systems, for example the behavior between
individual constituents and between the aggregate assembly and the surrounding environment
in response to an external load. Efforts involve multidisciplinary theoretical, analytical
and/or experimental approaches from disciplines such as engineering mechanics, material
science, physics and applied mathematics. Constitutive models that incorporate the
microstructural behavior of these heterogeneous anisotropic multiphase discrete systems
are theorized and experimentally demonstrated.
Particulate materials are ubiquitous, hence the research products from this program will
have a scientific impact on a diverse range of end users. This research will provide a
knowledge base from which analytical models can be developed to design and evaluate new
material processing technologies, and hence, more affordable aerospace structural
materials. Direct benefits to the military services include real-time subsurface target
detection and damage assessment on the battle field, improved earth penetrators and
precision guided munitions effectiveness, enhanced structural survivability and
vulnerability and smart infrastructure supporting systems capable of surviving
extreme blast loading. Much of the technology supporting these needs has been based on
empiricism. Therefore, the scientific contribution of this program will be a physically
based understanding of the behavior of a range of materials and analysis techniques to
predict their response to new loading regimes.
Structural Mechanics
The focus of the structural mechanics program is to investigate fundamental structural
principles over a broad length scale (i.e., nanometer
to meter scale). At the high end of this scale, an understanding of the aero-structural
and structural-acoustic behaviors of airframe, engine structures and launch vehicles is
desired. Nonlinearities in these systems are traced to the interaction of fluids and
structures, large amplitude vibration, system nonlinearity due to damping, and other
phenomenon. This research is expected to provide engineering information on airframe
failure from fluid flow disturbances and engine stall due to pressure variation. This
research seeks to provide answers to many system operational issues. Examples include
limit cycle oscillations and flutter on fixed-wing aircraft, engine compressor instability
and turbine failure.
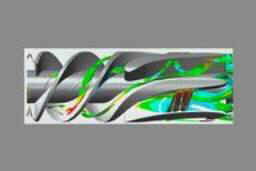
Results of this research have
been used by the Cessna Aircraft Company to predict the onset of flutter, understand post
flutter behavior, and develop active flutter control techniques. Also, researchers in the
universities are working with Air Force Research Laboratory and the Aeronautical Systems
Center (ASC) on these operational problems.
Smart and composite structures research involves coupling nonlinear structural mechanics
principles with advanced materials development, fluid mechanics, control theory, and
sensor/actuator technology, such as smart materials and microelectromechanical systems
(MEMS). This research will lead to the development and design of real-time monitoring and
self-correction techniques for enhancing system performance. For example, intelligent
materials and active structures are being developed which can continuously monitor damage
formation and growth in current and future aerospace structures. Continuous shape control
of aerodynamic surface may also be possible through a precise distribution of sensors and
actuators.
The anisotropy, inhomogeneity, and damage characteristics of emerging structural material systems dictate the
development of new solid mechanics and structural analysis principles critical for
performance prediction and material synthesis. Traditional mechanics of materials
principles do not capture the fundamentals that dictate the behavior of these advanced
material systems. One aspect of the structural mechanics program is to expand the
fundamental knowledge base to better understand the mechanics of deformation and damage of
aerospace structures. For example, engineers at both NASA and Goodyear Tire Company are
applying computational methodologies developed under this program to understand nonlinear
deformation of aircraft tires that lead to excessive wear.
Summary DoD
In summary, research in solid mechanics and structures is necessary for the design and
operation of future Air Force weapon systems, as well as the continuing operation of
existing systems, which are currently projected for use well beyond their original design
lifetimes. Under the Reliance Agreement, the Air Force has the lead responsibility for the
mechanics of high-temperature structural materials and particulate material systems and
fixed-wing aeroelasticity. The Army has primary responsibility for research in impact /
penetration mechanics, and rotary-wing aeroelasticity, while the Navy is the lead service
in the mechanics of thick-section composites, structural acoustics, and hydroelasticity.
|